Automate Your Way to Success
FANUC CNCs.
For high reliability, precision, speed
and simple operation

FA- Application Support
With a strong focus on technical and value addition, FANUC’s Application Support team works closely with machine tool builders, retrofitters and end user customers by applying design thinking principles and providing people-centric value engineering solutions across the Indian sub-continent.
Primary activities include:
- Hands on working with the machine tool builders, supporting the development of indigenous machines, as per the requirement of end users
- Regular visits to upskill end user customers contributes to adding value by educating them about latest FANUC technologies
- Closely working with retrofitters to provide cost effective solutions
With rising demand for higher productivity, superior precision, and accuracy, as well as low-cost manufacturing solutions in the Indian machine tool industry, end users are more focused on developments and innovations. In this scenario, adaptation of the latest control technologies is essential for end users. Keeping this in mind, FANUC works closely with end users to understand their requirements and provide customized solutions.
Exclusive Support For Various Applications. You
Name It, We Will Support It.
Parts Machining (Turning & Milling)
Cycle Time Optimization: Supports benchmarking the machine against a standard evaluation workpiece, ensuring all CNC functions are active, to achieve the optimum cycle time, with desired quality standards.
Turning Suite: Ready to use “off-the-shelf solution” for ease of operation by adding value to the users in the areas of tool life monitoring, tool load monitoring, cutting parameter calculation, energy consumption monitoring.
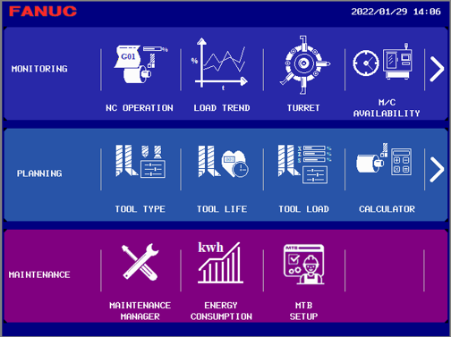
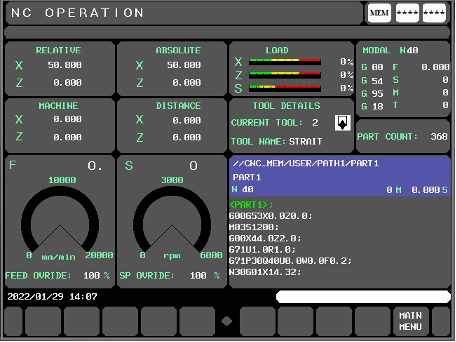
Die-Mould Machining: DM machining solutions are evaluated based on quality and accuracy. Machining results are dependent not only on CNC performance but also on other aspects like the machine itself, the CAM program, as well as selected cutting parameters. Deep experience in each of these areas helps in resolving field issues clearly. FANUC Digital Twin Technology ensures reproduce and identify the root cause of a problem. FANUC team supports in cutting trials to demonstrate technologies like Fine Surface Technology, provides training to customers not only on controllers but also machine-related aspects, CAM program generation and tooling related aspects – which are responsible for better surface finish.
Grinding Suite: This is applicable for various types of machines like OD Grinding, ID Grinding, Centreless Grinding and Surface Grinding. Customised dashboards with easy HMI help eliminate G Code Programming, thus reducing the development activity of MTBs & ensuring ease of operations for end users.
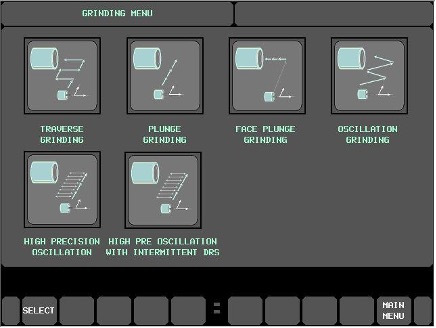
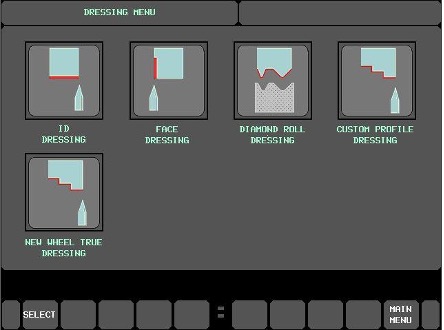
LASER Cutting: Work closely with MTBs for enhancing the machine performance by utilizing the high-speed synchronization of FANUC Servo Motors with LASER command. This results in achieving improvement in the cutting quality and reduction in cycle time. Support development of customized functions like:
- Multi-level piercing
- Easy program restart
- Easy to use machine interface
Friction Welding: Based on strong expertise in understanding the machine requirement, FANUC provides an exact solution to meet the spindle motor and drive requirement. This helps decelerate exactly as per the requirement during the welding process to get the best quality of welding.
Gear Manufacturing: High technology gear cutting machines proven with 0i Series CNC helps MTBs to offer their world class machines with best cost performance to benefit the users. The 0i Series CNC has been interfaced and tested for its best performance to match gear quality with DIN7~8. FANUC also offers gear skiving of hardened gears.
Railways Wheel Machining: This is a unique process that analyses wear patterns of used railway wheels. Thereafter, it suggests the optimum profile which can be machined. FANUC offers complete solutions with the necessary software development for Railways Wheel Machining.